Запись второго вебинара, посвященного полиолефиновым пленкам, доступна по ссылке.
Часть 2.1. Рукавные пленки
Наиболее распространенным способом производства полимерных пленок является экструзия. В зависимости от устройства экструзионной линии можно получать три основных типа пленок:
- рукавные пленки (раздувные пленки);
- каст-пленки (плоскощелевые пленки);
- биаксиально-ориентированные пленки.
Преимущества и недостатки каждого типа пленок и технологий их производства приведены в таблице:
Рукавные пленки |
Каст-пленки |
Биаксиально-ориентированные пленки |
|
---|---|---|---|
Преимущества |
Сбалансированные физико-механические свойства Не требуется обрезка кромок Небольшие инвестиции в оборудование Получение толстых пленок, мешков, термоусадочных пленок
|
Высокая эффективность охлаждения Высокая скорость производственного процесса Отличные оптические свойства Низкая разнотолщинность
|
Высокая эффективность охлаждения Высокая скорость производственного процесса Отличные оптические свойства Низкая разнотолщинность Повышенная прочность
|
Недостатки |
Ухудшенные оптические свойства Высокая разнотолщинность Низкая скорость линии
|
Ухудшенные физико-механические свойства Требуется обрезка кромок Трудность регулировки ширины пленки в широком диапазоне
|
Необходимость обрезки кромок Меньшая гибкость для изменения ширины пленки Большие инвестиции Низкое сопротивление раздиру
|
Глоссарий
Экструзия – процесс формования изделий из полимеров (или композиций на основе полимеров) путем продавливания расплава через экструзионную головку с формующими каналами определенного профиля.
Разнотолщинность – нестабильность толщины пленки.
Ориентация пленки – процесс модификации пленки с целью повышения ее прочности, в ходе которого пленку в нагретом состоянии вытягивают (деформируют) в одном или двух направлениях.
В этой статье мы более подробно остановимся на технологии производства и способах применения рукавных пленок. Каст-пленки и биаксиально-ориентированные пленки будут рассмотрены в следующем материале.
Рукавные пленки
Технологическая схема производства рукавных пленок и ее основные узлы
Процесс производства протекает следующим образом: гранулы полимерного сырья, нередко вместе с различного рода функциональными добавками, с помощью системы дозирования, в заданном согласно рецептуре количестве поступают в экструдер, где происходит плавление, смешение и гомогенизация. После этого расплавленная полимерная композиция поступает в экструзионную фильеру, в которой расплав равномерно распределяется, приобретает кольцевое сечение и выходит через отверстие в форме рукава. Одновременно внутрь выходящего полимерного рукава подается воздух, под воздействием которого рукав раздувается до необходимого размера и охлаждается. Далее пленочный рукав посредством тянущих валков движется вверх, продолжая охлаждаться, затем складывается в сдвоенное полотно, при необходимости проходит стадию активации, после чего пленка может поступать на намотчик в виде целого рукава либо разделяться на два полотна для намотки в отдельные рулоны.
Одним из важнейших элементов линии для производства рукавных пленок является экструдер – это оборудование, предназначенное для плавления и гомогенизации полимерной смеси, а также для транспортировки расплава к экструзионной фильере при постоянных температуре и давлении. Экструдер состоит из обогреваемого материального цилиндра, внутри которого находится шнек, приводимый в движение электродвигателем.
Экструдер можно условно разделить на три зоны: зона загрузки, зона плавления (пластикации) и зона дозирования. Температуры в разных зонах экструдера определяются свойствами перерабатываемого материала. Обычно температура материального цилиндра плавно возрастает от загрузочного отверстия к фильере.
В большинстве современных линий производства полиолефиновых пленок используются одношнековые экструдеры, обеспечивающие достаточное перемешивание при более низкой стоимости в сравнении, например, с двухшнековыми. Среднее соотношение длины и диаметра таких экструдеров – 28–30. Конструкция шнеков экструдера может быть разной, для улучшения гомогенизации в шнеках могут быть специальные зоны для смешения.
Экструзионная фильера – один из самых важных и дорогих узлов технологической линии производства пленок. Расплав из материального цилиндра экструдера через фильтр расплава поступает в экструзионную головку снизу по угловому цилиндрическому каналу и рассекается на отдельные потоки, которые затем сливаются. Для предотвращения образования стыковых полос в местах соединения потоков расплава на дорне предусматривают спиральные распределительные каналы, турбулизующие и гомогенизирующие его. Далее расплав приобретает кольцевое сечение и выдавливается через формующий зазор фильеры.
Существует несколько видов выдувных фильер, принципиально отличающихся по конструкции и способу соединения потоков расплава от разных экструдеров. Один из них – это Stack Die (Pancake Die). В этой фильере каждый так называемый «блин» служит для формирования отдельного слоя расплава. Чем больше слоев, тем больше необходимо использовать «блинов». «Блины» располагаются друг на друге и жестко закрепляются между собой.
Другой распространенный в настоящее время вид фильеры для производства рукавных пленок – Spiral Mandrel Die. Потоки расплава от разных экструдеров поступают в такую фильеру на одном уровне по высоте, но проникают на разную глубину внутри фильеры. Затем каждый слой перемещается по своему каналу, также проходя область фильеры со спиральным распределением, и вблизи от выхода из фильеры происходит объединение слоев.
Stack Die (Pancake Die) |
Spiral Mandrel Die |
|
---|---|---|
Преимущества |
Традиционная проверенная конструкция Легкость изготовления фильеры Вариативность с точки зрения размеров и количества слоев в фильере путем изменения количества «блинов» в ее составе
|
Отсутствие предела давления расплава в фильере Снижение разнотолщинности пленки Большая скорость переходов между материалами Большая скорость смены красителей Меньшее время пребывания расплава в фильере Возможность реализации соэкструзии в одной пленке очень тонких слоев (до 1 мкм) Большие каналы для подачи воздуха в систему внутреннего охлаждения рукава для большей производительности
|
Недостатки |
Существенные ограничения по давлению расплава (до 450 бар) Неравномерность потока расплава в каждой спирали Невозможность добиться однородности обработки поверхности каждого канала Большое количество слоев негативно сказывается на однородности давления в фильере Ограничение по количеству подключенных экструдеров
|
Сложность и дороговизна изготовления фильеры |
Для различных видов полиэтилена существуют различия в конструкции зазоров фильер. Для производства пленок из полиэтилена низкой плотности (LDPE) обычно используют фильеры с узким зазором (0,6–1 мм), для линейного полиэтилена низкой плотности (LLDPE) необходим широкий зазор (1,8–2,5 мм), а для полиэтилена высокой плотности (HDPE) – средний (1–1,5 мм).
После выхода из экструдера рукав пленки раздувается и охлаждается воздухом. Стадия охлаждения – это лимитирующая стадия процесса производства пленки, то есть скорость охлаждения ограничивает производительность линии. У воздуха низкая теплоемкость, что затрудняет процесс охлаждения. Рукав можно охлаждать тремя способами: снаружи, изнутри и комбинированно. Комбинированное охлаждение ускоряет процесс и способствует увеличению производительности линии.
Особенности формирования рукава для LDPE и HDPE
Формирование рукава для полиэтиленов низкой и высокой плотности проходит в разных условиях. Для LDPE и LLDPE требуется низкая линия кристаллизации и высокая скорость охлаждения. Для HDPE, напротив, нужна высокая линия кристаллизации и низкая скорость охлаждения. HDPE сложнее в переработке, и рукав формируется в виде «бокала вина».
Самым доступным решением является охлаждающее кольцо без контроля профиля, которое создает два воздушных потока, охлаждающих расплав снизу вверх. Более современное воздушное кольцо с контролем профиля синхронизировано с толщиномером, что позволяет тонко подстраивать толщину пленки по всей окружности рукава. Такая же система используется в подъемном воздушном кольце, которое характеризуется большей эффективностью охлаждения. Подъемное кольцо также позволяет проводить процесс ориентации пленки при более низких температурах, что улучшает ее физико-механические свойства.
Система внутреннего охлаждения рукава (IBC, internal bubble cooling) значительно улучшает работу технологической линии. Она обеспечивает воздухообмен внутри пленочного пузыря, дает возможность принудительного охлаждения пленки внутри пузыря, осуществляет автоматический контроль и поддержку раздува пузыря посредством автоматического установления коэффициента раздува (BUR, blow-up ratio). Линии, оборудованные системой внутреннего охлаждения рукава, обладают рядом преимуществ:
- уменьшение количества отходов при пуске и выводе на режим;
- существенное повышение производительности;
- улучшение оптических и физико-механических свойств пленки;
- минимизация флуктуаций ширины пленки.
Полиэтилен обладает более высокой удельной теплоемкостью (1,8–2,3 кДж/кг∙К) по сравнению с другими полимерами (0,9–1,5 кДж/кг∙К). Из-за более высокой теплоемкости требуется высокая (длинная) секция охлаждения – при недостаточном охлаждении рукав полиэтиленовой пленки может слипнуться и не раскрыться.
После охлаждения пленки может проводиться обработка или активация ее поверхности. Полиолефины – неполярные полимеры, а это означает, что полярные соединения плохо смачивают поверхность таких полимеров. Это важно, например, в процессах печати – более полярные по своей природе печатные краски плохо закрепляются на необработанной поверхности пленки. Для увеличения поверхностного натяжения пленок обычно используют обработку ее поверхности коронным разрядом, также существуют методы активации пламенем и плазмой. Следует помнить, что любой вид активации поверхности пленки имеет временный эффект, постепенно пропадающий ввиду миграции на поверхность пленок добавок (например, скользящей добавки – эрукамида) и постоянного движения макромолекул самого полимера, поэтому печать на пленке нужно провести в течение нескольких дней после обработки. Также можно перед печатью повторно проводить активацию.
Производство некоторых типов выдувных пленок может включать дополнительные этапы ориентирования молекул полимеров. Этого можно достичь дополнительным раздувом уже охлажденного рукава по технологии double bubble или triple bubble: после первого охлаждения рукав пленки снова нагревается и растягивается, но уже при более низкой температуре, что позволяет провести дополнительное ориентирование макромолекул полимера. Полученные таким образом пленки обычно используются для производства термоусадочных пленок для упаковки продуктов.
Базовые рекомендации по переработке марок полиэтилена СИБУРа для производства рукавных пленок
Параметр |
LDPE |
LLPDE |
HDPE |
---|---|---|---|
Температура расплава |
180–190°С |
200–220°С |
200–220°С |
Коэффициент раздува (BUR) |
2–3 |
3,5–4 |
|
Высота линии кристаллизации (FLH) |
(2–3)*D1 |
(7–12)*D1 |
|
Зазор фильеры |
0,6–1,0 мм |
1,8–2,5 мм |
1,0–1,5 мм |
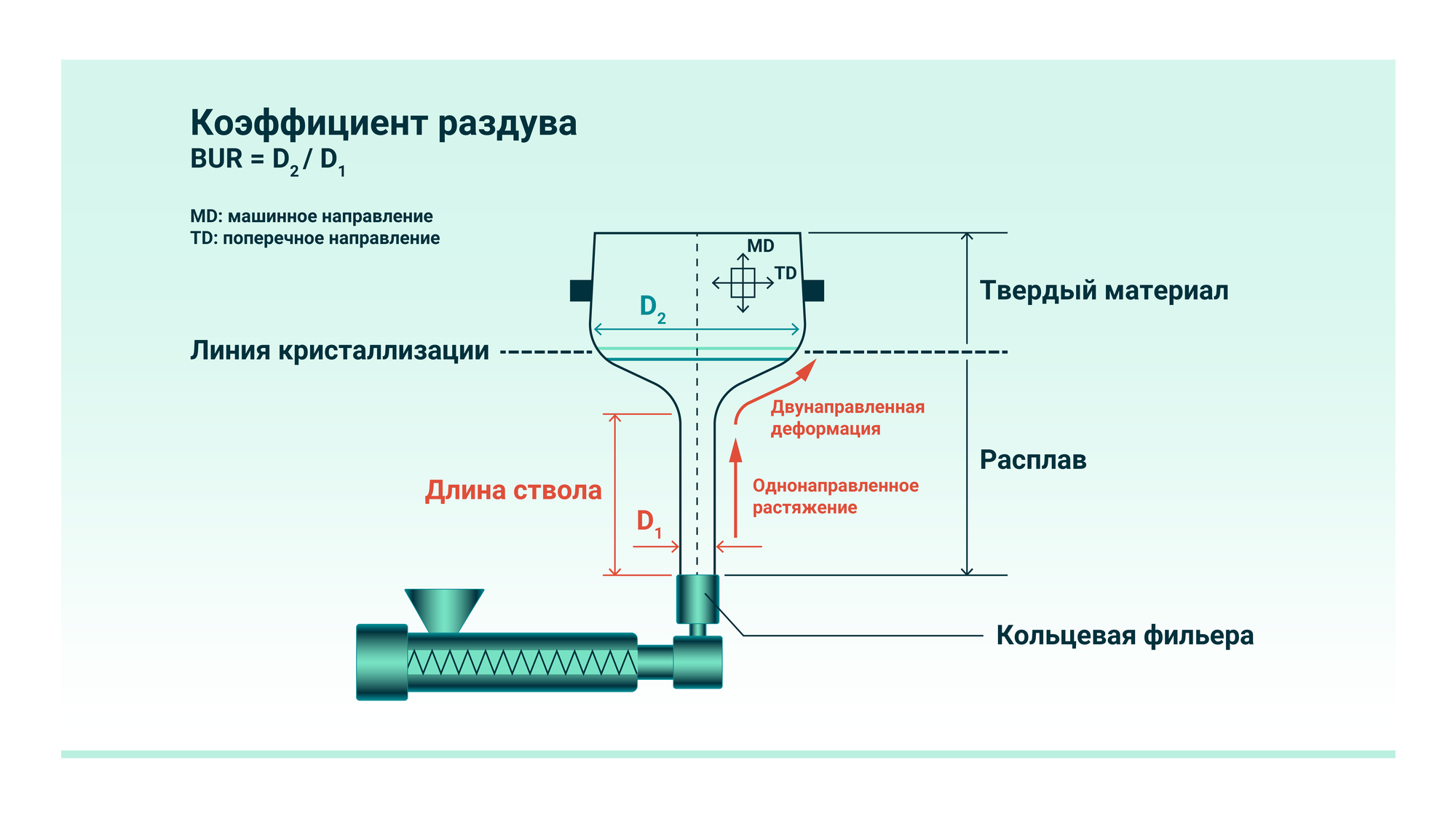
Ассортимент полиолефинов для производства рукавных пленок, выпускаемый на предприятиях СИБУРа, представлен в каталоге СИБУРа сегмента «Упаковка»
Наиболее распространенные виды рукавных пленок
Пленки для ламинации
Ламинат – сочетание двух или более пленок, соединенных вместе и образующих сложную многослойную структуру, с целью достигнуть комплекса определенных характеристик упаковки, отсутствующих у каждой из пленок в отдельности (свариваемости, барьера, прочности, оптических свойств). К пленкам для ламинации обычно предъявляются следующие требования:
- хорошие механические свойства;
- хорошие оптические свойства (прозрачность, блеск, мало гелей);
- хорошие сварные свойства;
- хорошие органолептические свойства (отсутствие запаха, безопасность контакта с пищей);
- толщина 30–150 мкм;
- жесткость, сопротивление проколу;
- барьер к воде.
Полиолефиновые пленки для ламинации обычно применяются для изготовления многослойных гибких упаковок (дой-паки, чай и кофе, глубокая заморозка, корма для домашних животных, барьерные пленки, гигиенические средства).
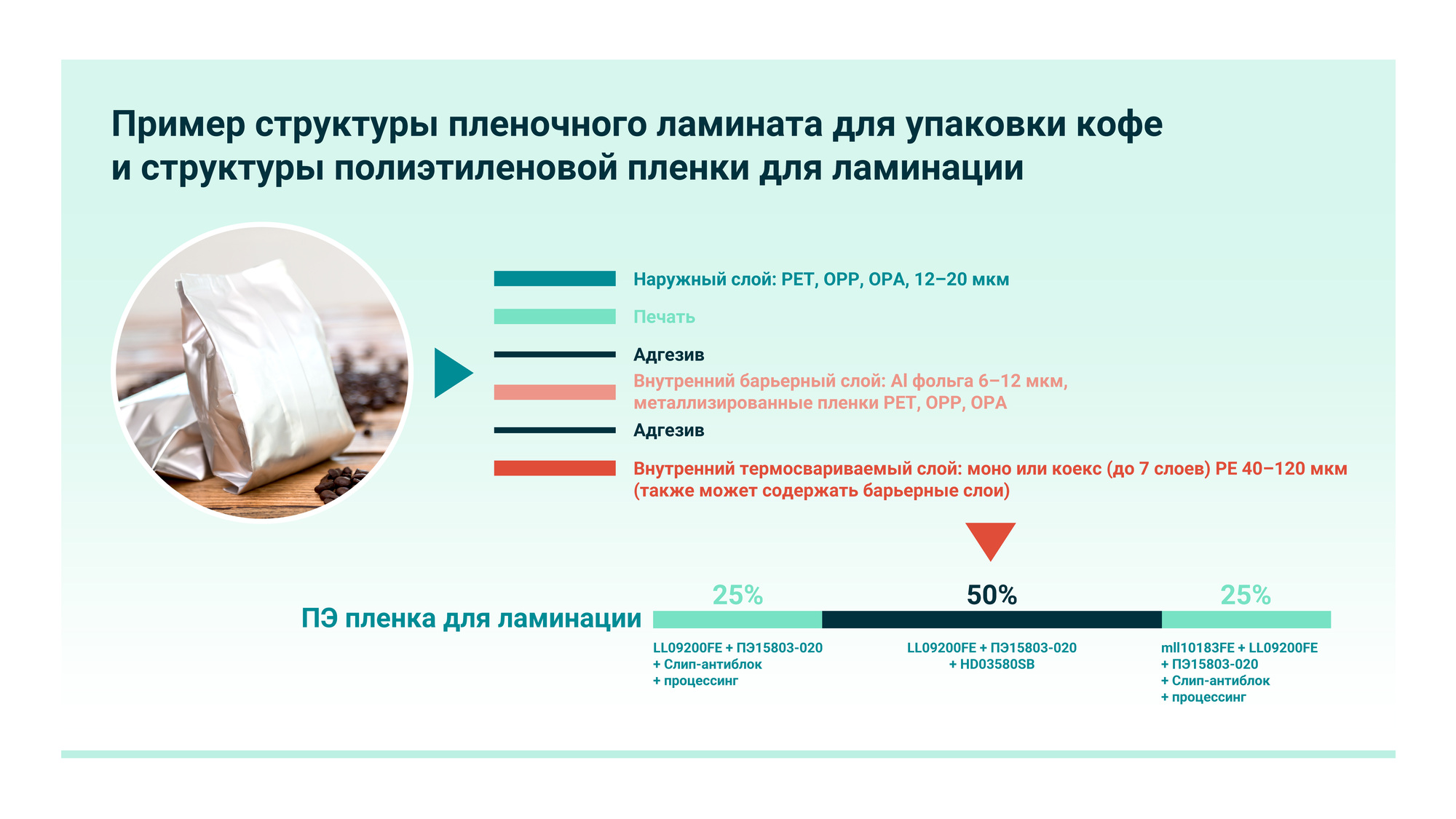
Термоусадочные пленки
Термоусадочными называются полимерные пленки, способные сокращаться под воздействием температуры, превышающей температуру размягчения полимера. Для промышленной упаковки паллет используются термоусадочные пленки толщиной от 80 до 200 мкм, для групповой упаковки товаров – от 30 до 70 мкм. К термоусадочным пленкам обычно предъявляются следующие требования:
- низкое усадочное напряжение при повышенных температурах (отсутствие разрыва пленки в процессе усадки);
- высокое усадочное напряжение в холодном состоянии (высокая удерживающая способность);
- баланс усадки в обоих направлениях (легкость контроля усадки);
- хорошие физико-механические свойства (прочность, жесткость);
- низкая температура сварки;
- возможность качественной печати;
- хорошие оптические свойства.
Для термоусадочных пленок используются следующие полимеры:
- LDPE – базовый материал, обуславливающий усадку;
- HDPE – для повышения жесткости пленки, для увеличения усадки в направлении экструзии (содержание не более 25–30%, иначе ухудшаются оптические свойства и перерабатываемость);
- LLDPE – для улучшения сварных, оптических и физико-механических свойств;
- mLLDPE – для улучшения сварных, оптических и физико-механических свойств.
Пленки сельскохозяйственного назначения (парниковые, пленки для мульчирования, сенажные)
Выдувные полиэтиленовые пленки широко используются в сельском хозяйстве, прежде всего для покрытия теплиц, для мульчирования и для упаковки сена.
Парниковые пленки могут быть как односезонными, так и многосезонными. Односезонные парниковые пленки обычно имеют один слой толщиной от 80 до 150 мкм, состоящий из смеси LDPE (около 70–80%) и LLDPE (20–30%). Многосезонная пленка для крупных теплиц имеет большую толщину, от 120 до 250 мкм, и трехслойную структуру. В состав парниковых пленок входят преимущественно низкоиндексные марки LDPE с добавлением небольшого количества LLDPE. Также иногда используют сополимер этилена и винилацетата (EVA), поскольку его меньшая проницаемость для инфракрасного излучения позволяет дольше сохранять тепло внутри теплиц. Многосезонные тепличные пленки должны иметь усиленную рецептуру светостабилизации, в ряде случаев обладать антифог-эффектом и высокой прозрачностью для солнечных лучей.
К парниковым пленкам предъявляются следующие требования:
- стойкость к УФ-излучению;
- отсутствие запотевания (антифог-эффект);
- хорошие физико-механические свойства;
- прозрачность для необходимого растениям света;
- толщина 80–250 мкм.
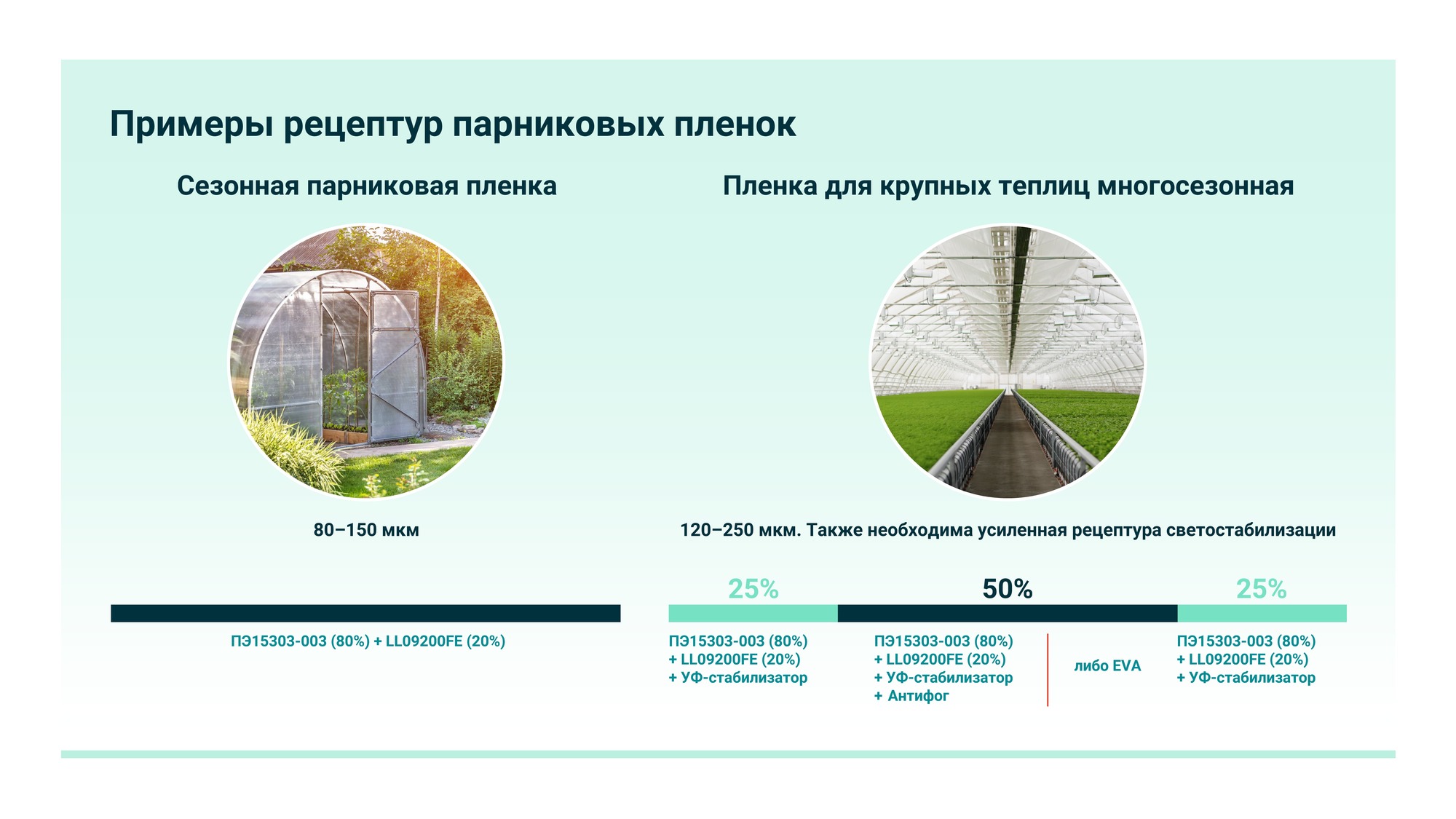
Пленки для мульчирования могут быть однослойными или многослойными. Они должны задерживать свет, для этого при изготовлении используются различные мастербатчи (концентраты красителей). Срок службы этих пленок составляет всего 2–4 месяца.
К пленкам для мульчирования предъявляются следующие требования:
- светонепроницаемость (эти пленки могут быть черными, белыми, цветными, металлизированными);
- достаточные физико-механические характеристики;
- свето- или биоразлагаемость (срок службы 2–4 месяца);
- толщина 15–80 мкм.
Сенажные пленки используют для упаковки сена, для его продолжительного хранения и удобной транспортировки. Этот вид пленок имеет повышенные требования к ряду свойств и к качеству, так как влага, проникшая через пленку к сенажу, может привести к его гниению. Также требуется стойкость к УФ-излучению. Средний слой может быть изготовлен из металлоценового LLDPE (mLLDPE). Наружные слои состоят преимущественно из mLLDPE с добавлением адгезионных полимеров (PIB) или пластомеров на основе полиэтилена для липкости.
К сенажным пленкам предъявляются следующие требования:
- стойкость к проколу, высокие стягивающие свойства;
- эластичность и растяжимость;
- хорошая липкость (cling-эффект);
- стойкость к УФ-излучению;
- повышенные барьерные свойства;
- толщина 20–25 мкм.
Пленки для производства пакетов
Крупным сегментом применения рукавных пленок, с котором все мы сталкиваемся довольно часто, являются пакеты. Более жесткие пакеты типа «майка» производят из HDPE, иногда с добавлением небольшого количества LLDPE для улучшения свариваемости. Пакеты, имеющие глянцевый внешний вид, делают из смеси LDPE и LLDPE.
К пленкам для пакетов предъявляются следующие требования:
- высокие прочностные свойства;
- способность к тепловой сварке;
- возможность качественной печати.
Пленки для производства упаковочных мешков (для удобрений и полимеров)
Из рукавных пленок делают мешки для тяжелых сыпучих грузов. Прочные мешки из полиэтилена хорошо подходят для упаковки готовой продукции и сырья в форме гранул, порошка и т. п. Пленки для производства мешков обычно состоят из 3–5 слоев. Толщина таких пленок варьируется в пределах 100–160 мкм, наблюдается тренд снижения толщины.
К пленкам для мешков предъявляются следующие требования:
- хорошие механические свойства (стойкость к проколу и раздиру, жесткость);
- возможность качественной печати;
- хорошие сварные характеристики;
- защита от УФ-излучения.
Заключение
Благодаря простой схеме производства и сравнительно невысоким инвестициям в оборудование, рукавные пленки получили широкое распространение и применяются во многих отраслях экономики. Из них производят разнообразную продукцию: от упаковочных пакетов до сельскохозяйственных пленок. В этом материале мы рассмотрели особенности производственного процесса, преимущества и недостатки рукавных пленок, а также подробно разобрали некоторые примеры их применения с указанием рецептур и основных требований.
Комментарии (0)