Brief history of film materials
A film is a flexible polymer material with a thickness below 300 µm. It was invented relatively recently, and its history began just in the middle of the 19th century. The first films were made from celluloid – a plastic material derived from cellulose nitrate, discovered in 1855 by the British metallurgist Alexander Parkes. Celluloid has several flaws, therefore the search for other materials for films continued. Science was quick to explore new opportunities, so with time more types of plastics suitable to be used in films emerged.
The History of Films
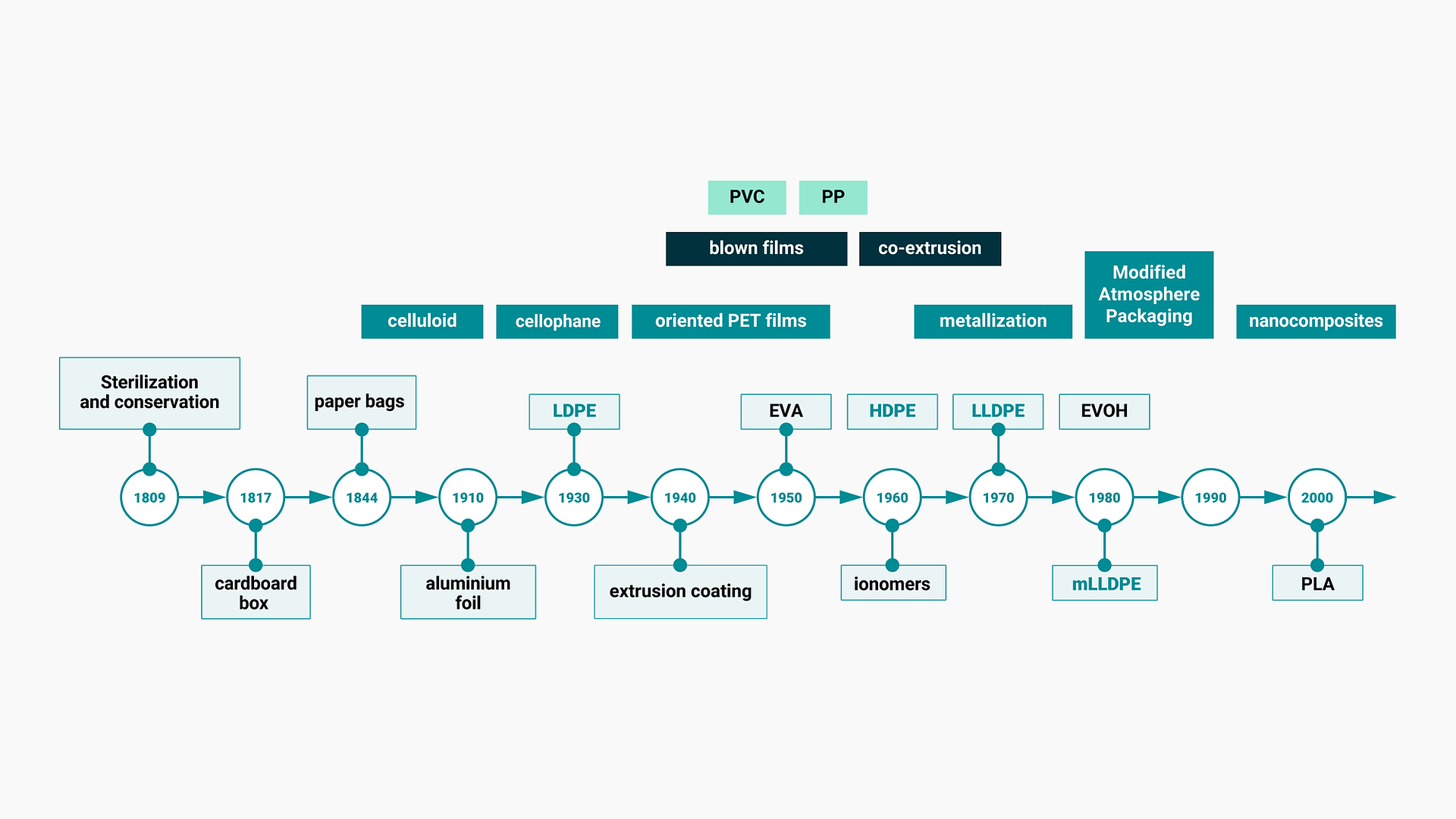
Films have multiple usages:
- Packaging for industrial products and semi-finished products.
- Technical films for industry and agriculture.
- Packaging for various types of non-edible products sold in retail.
- Packaging for food and edible raw materials.
- Packaging for medical, hygienic, and pharmaceutical products.
The vast majority of films are used in packaging materials. Different goods require different types of packaging with specific properties. The properties of a film are determined by what it’s made of – the polymer material. Let’s take a closer look at polymers.
A few facts about polymers
Polymers are macromolecular compounds with large molecular masses (ranging from several thousand to several million) consisting of many repeating similar or different subunits – monomers, which are chemically bound into lengthy macromolecules.
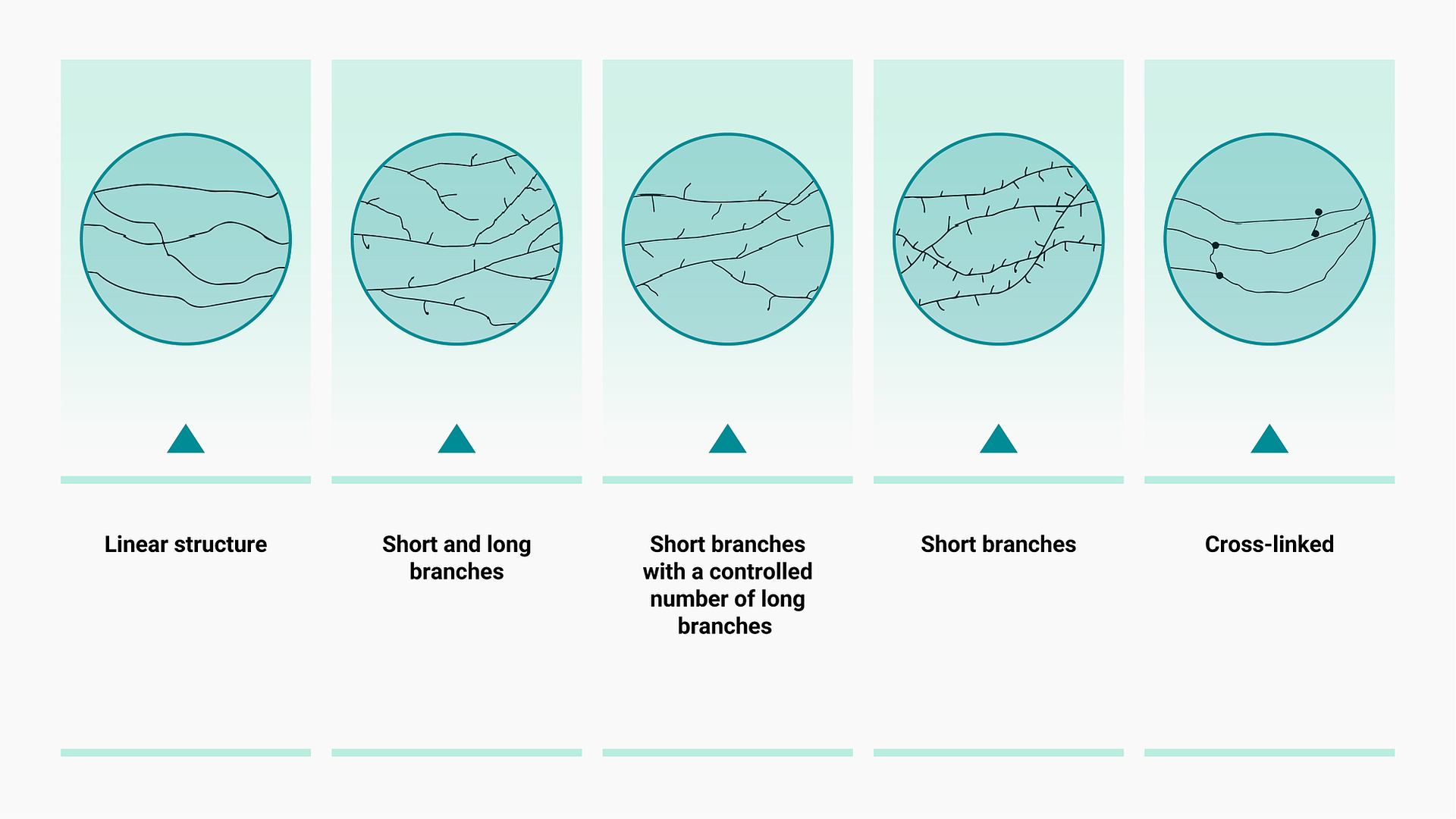
The number of monomers in a polymer macromolecule is called the degree of polymerization. The majority of polymers used in industry have a degree of polymerization in the range between 100 and 10000. The properties of a polymer are determined primarily by its molecular mass and degree of crystallinity.
Polymers are semi-crystalline compounds, part of their molecules is ordered and form a crystalline phase, whereas the other part is unordered and amorphous. The mass fraction of a compound’s crystalline phase is called the degree of crystallinity. In polymers, the degree of crystallinity never reaches 100% and depends on several factors which include the type of polymer (and its co-polymers, if there are any) and the catalysts which were used in its manufacturing process.
What are polyolefins and how they are used in films?
Polyolefins are polymers derived from olefins – unsaturated hydrocarbons with double bonds. The most common polyolefins used in the manufacturing of modern films are polyethylene and polypropylene. They are used in the production of the main types of films:
- LDPE (low-density polyethylene).
- LLDPE (linear low-density polyethylene).
- HDPE (high-density polyethylene).
- VLDPE, или POP (very low-density polyethylene).
- ULDPE или POE (ultra low-density polyethylene).
- PP (polypropylene).
- r-PP (polypropylene random copolymer).
- Block-PP (polypropylene block-copolymer).
Polyolefins’ popularity as a raw material for films can be explained by the following facts: these films are easily processed, they have low mass, high strength and tear resistance, they are flexible even in low-temperature conditions, they have high chemical resistance and cost relatively cheap when compared to other types of polymers. It’s also important to point out that ethylene and propylene are some of the most widespread and processible monomers in the world.
Type | Name | Structure | Characteristics and copolymers | Manufacturing process | Properties |
---|---|---|---|---|---|
LDPE | low-density polyethylene | Branched (autoclave LDPE is more branched than tubular reactor LDPE) | ρ = 0,915 – 0,935 g/cm3 Wide MWD | Radical
polymerization:
|
|
LLDPE | linear low-density polyethylene | Linear (~20 short side branches per 1000 carbon atoms) | ρ = 0,910 – 0,935 g/cm3 Narrow MWD Butene, hexene, octene | Catalytic polymerization:
|
|
HDPE | high-density polyethylene | Linear (0-6 short side branches per 1000 carbon | ρ = 0,935 – 0,965 g/cm3 Wide MWD | Catalytic
polymerization:
|
|
VLDPE (POP) | very low-density polyethylene | A high amount of short side branches | ρ = 0,890 – 0,910 g/cm3 Narrow MWD Butene, hexene, octene | Metallocene catalysed polymerization |
|
ULDPE(POE) | ultra low-density polyethylene | A very high amount of short side branches and co-monomer content | ρ < 0,890 g/cm3 Narrow MWD Butene, hexene, octene | Metallocene catalysed polymerization |
|
PP | polypropylene | Linear polymer. The location of methyl
groups determines the type of the polymer:
|
ρ = 0,905 g/cm3 | Catalytic polymerization: Ziegler–Natta |
|
r-PP | polypropylene random copolymer | Linear with random locations of ethylene groups in the chain | ρ = 0,905 g/cm3 Ethylene, butene | Catalytic polymerization: Ziegler–Natta Metallocenes |
|
BlockPP | polypropylene block-copolymer | Linear with arranged locations of ethylene groups in the chain (blocks) | ρ = 0,905 g/cm3 Ethylene | Catalytic polymerization: Ziegler–Natta |
|
How characteristics of polymers impact the properties of films
Film properties depend on the characteristics of the polymers from which they are made of. Let’s examine the key characteristics of polymers.
Molecular weight
The average molecular weight of a polymer is determined by the melt flow index (MFI). MFI measures the ease of flow of the melt of a thermoplastic polymer. It is defined as the weight of the polymer in grams flowing in 10 min through a die of specific diameter and length by a pressure applied by a given weight at a given temperature. Low MFI means high viscosity and higher molecular weight. High MFI, on the contrary, is observed for polymers with low viscosity and lower molecular weight.
Density, branching, and melting point
The density of a polymer is related to its degree of crystallinity and determines its ability to crystallize. If a polymer is linear and doesn’t have branches (like HDPE), its density and degree of crystallinity are high. When the density of a polymer increases, so do the following characteristics:
- rigidity
- tensile strength
- softening point
- fold retention
- curling
- chemical resistance
- heat resistance
- barrier properties
If a polymer contains many short and/ or long branches (like LDPE), its density and degree of crystallinity are low. When the density of a polymer decreases, the following characteristics increase:
- tear strength
- puncture resistance
- impact viscosity
- friction coefficient
- optical properties
Molecular weight distribution (MWD)
Synthetic polymers consist of molecules with different masses, which is explained by the statistical nature of polymerization. The ratio of molecules with different molecular masses in a polymer is defined as molecular weight distribution. Gel-penetrating chromatography or fractioning can be used to determine MWD, but it’s possible to estimate it by determining a polymer’s MFI under different loads: the more the ratio of MFI, the wider is MWD.
Wider MWD is associated with the following positive effects:
- increased ability to process the polymer (the pressure of the melt is lower, which decreases the gear load, since the molecules with lower molecular weight act like lubricants)
- the durability and stability of melt increase
- fewer surface defects of the film (sharkskin)
- orientation of the polymer is increased
Negative effects attributed to wider MWD:
- less durable welding joints
- worse optical properties
- lower ripping resistance
- low-weight molecules can form residues on the surface of the equipment
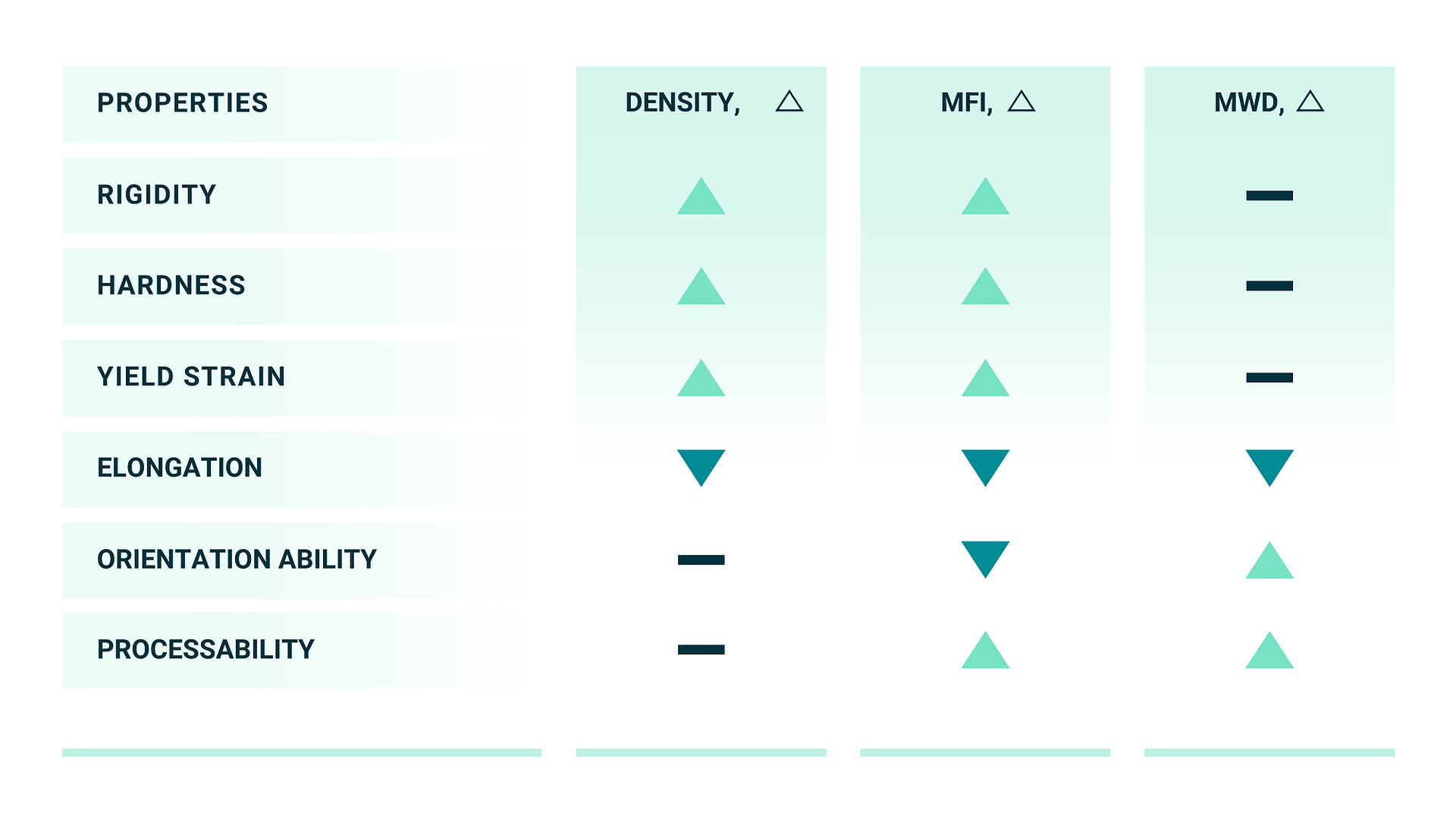
MFI — melt flow index
MWD — molecular weight distribution
Why are additives used in films?
Additives are intended to improve various properties of polymers. The following requirements must be adhered to regardless of additive function:
- good compatibility with the polymer
- no effects which could contribute to polymer destruction
- resistance to water exposure
- lack of smell
- safety for health and environment
- convenient dosing and usage
Additives used in polyolefin films can be divided into two broad categories:
- additives which increase the stability and processability of the polymer
- functional additives which improve certain properties of the polymer
The following types of additives are used to increase stability:
Antacids | They neutralize the free acidity of catalyst residues used in polymers manufacturing, prevent equipment corrosion |
Antioxidants | They prevent oxidation and destruction of the polymer during processing, storage, and usage. They maintain the physical, mechanical, and optical properties of the film |
UV stabilizers | They protect the polymer from UV radiation exposure, maintain the physical, mechanical, and optical properties of the film, protect the packaged product |
Processing additives | They ease the processing, remove extrusion defects, and reduce carbonization and the content of gels |
The common goal of these additives is to prevent molecular mass and structural changes in the polymer. The consistency of the polymer’s properties enables the use of it as intended for as long as possible. It expands the recycling window – the ability to reuse the polymer after the initial product has lost its consumer properties.
Functional additives used in polyolefin films include:
Slip agents | Reduce the coefficient of friction, exclude sticking and blocking of films |
Anti-blocking additives | Reduce sticking (blocking) of layers of film in a roll |
Antistatic agents | Prevent the accumulation of electrostatic charges, and dust settling, and exclude film blocking |
Nucleating agents | Change the crystallinity of the polymer and the optical and mechanical properties of the film. Does not dissolve in polymer |
Antifog additives | Prevent film fogging due to water vapour condensation |
Gas absorbents | Absorb gases inside film packaging (ethylene, oxygen) |
Clarifying agents | Reduce haziness and increase the transparency of the film due to crystal size change. Dissolve in polymer |
Antimicrobial additives | Prevent the development of microorganisms, protect the packaged product |
Pigments and dyes | Gives colour to the film, in some cases protects against UV radiation (titanium dioxide) |
Modifying agents | Change any of the properties of the film, for example, increase rigidity, mattness, stickiness |
Foaming agents | Reduce the density of the film, form a porous structure |
Fillers | Affect the polymer’s mechanical properties, increase opacity, and change the polymer’s barrier properties. Reduce cost |
Anti-blocking and slip agents are often used together. Anti-block agents prevent film surfaces from sticking together in a roll, creating a rough surface that forms an air gap between film layers. Slip agents migrate to the film surface and form thin layers that reduce the coefficient of friction between film layers.
Polyolefins for film manufacturing produced by SIBUR’s enterprises
SIBUR’s enterprises manufacture both polymers (raw materials for film manufacturing) as well as finished film materials. The assortment of polyolefins produced by SIBUR includes LDPE, LLDPE, mLLDPE, HDPE, EVA (ethylene-vinyl acetate) copolymers, HPP, RPP, and IPP. SIBUR BIAXPLEN manufactures biaxially oriented polypropylene (BOPP) films which are highly durable, flexible and have good optical properties.
Name | Manufacturer | MFI, g/10 min | Density, g/cm3 | Main characteristics | Recommended uses | |
---|---|---|---|---|---|---|
LDPE for blown film | ||||||
15803-020 | Tomskneftehim | 2,0 | 0,921 | Base grades for film production | Films for food and non-food packaging | |
15813-020 | Kazanorgsintez | 2,0 | 0,919 | |||
LD 20220 FE | Tomskneftehim | 2,0 | 0,926 | Improved optical properties, better compatibility with LLDPE | ||
10803-020 | Kazanorgsintez | 2,0 | 0,918 | Base grades for film production | Heat-shrinkable film, films for food and non-food packaging | |
15303-003 | Tomskneftehim | 0,3 | 0,922 | |||
15313-003 | Kazanorgsintez | 0,3 | 0,920 | |||
LD 03210 FE | Tomskneftehim | 0,3 | 0,926 | Improved optical properties and ripping resistance | ||
LD08220 FE | Tomskneftehim | 0,8 | 0,921 | Improved optical properties, excellent compatibility with LLDPE | Multilayer films for lamination, general-purpose films | |
LLDPE for blown and stretch film | ||||||
LL 09200 FE | Zapsibneftekhim | 2,0 | 0,920 | High physical and mechanical properties, excellent welding, excellent optical properties | Films for food and non-food packaging, films for lamination, industrial films | |
LL20211 FE | 0,920 | |||||
LL20211 FE | 0,921 | Improved physical, mechanical, and optical properties, excellent anti-blocking and slip properties of films | Films for food and non-food packaging, films for lamination | |||
LL 30200 FE | High physical and mechanical properties, excellent optical properties | Mono- and multilayer flat slit films, stretch films | ||||
LL30203FH (PE 5118 QM) | Nizhnekamskneftekhim | |||||
LL30203FE (F2230) | Kazanorgsintez | |||||
mLLDPE, special LLDPE for blown film | ||||||
mLL10183FE (F2010 M) | Kazanorgsintez | 1,0 | 0,920 | Increased puncture resistance, good welding, good optical properties | FFS film, stretch hood film, films for lamination | |
LL30183FE (F2030 M) | Kazanorgsintez | 3,0 | 0,920 | High pre-stretch, good optical, physical and mechanical properties | Mono- and multilayer stretch films, agricultural and high-strength films | |
LL 03320 FE | Kazanorgsintez | 0,3 | 0,931 | High physical and mechanical properties in combination with good processability. High strength indicators | Multilayer films, FFS films, films for lamination, heat-shrinkable films | |
HDPE for blown film | Processing method | |||||
HD10500 FE | Zapsibneftekhim | 10,0 | 0,950 | High physical and mechanical properties, wide MWD | Mono- and multilayer films, bags, garbage bags, geosynthetic materials | Film extrusion |
HD12443 FE(293 285Д) | Kazanorgsintez | 12,0 | 0,946 | |||
HD12503 FE(273 285 Д) | Kazanorgsintez | 12,0 | 0,951 | Extrusion blow moulding | ||
HD80520 FE | Zapsibneftekhim | 8,0 | 0,952 | Improved physical and mechanical properties, good processability, film roll stability | Thin films, bags, industrial packaging. Use in blends with low-flow LDPE grades in heat-shrinkable film formulations | Film extrusion |
HD 03580 SB | Zapsibneftekhim | 0,3 (21,6 kg/ 2,16) | 0,958 | Improved physical and mechanical properties, good processability | Use in blends with low-flow LDPE grades in heat-shrinkable film formulations, grain storage sleeves | Extrusion blow moulding |
Special LDPE for cast film, foaming and lamination segment | ||||||
LD 40251 FE | Tomskneftehim | 4,0 (190˚С, 2,16 kg) | 0,925 | Excellent optical properties and processability | Mono- and multilayer cast films for food contact materials | |
LD 40200 FA | 4,0 (190˚С, 2,16 kg) | 0,921 | Increased capacity, flow stability at high speeds | Foam products, lamination | ||
11503-070 | Kazanorgsintez | 7,0 (190˚С, 2,16 kg) | 0,920 | Applying coatings with low deposition rates | Lamination of paper, cardboard, and aluminium foil; food and non-food packaging | |
LD 50210 EC (LA2150) | 5,0 (190˚С, 2,16 kg) | 0,921 | High deposition rates, low extractives content, improved rheological properties | |||
LD 75210 EC (LA2175) | 7,5 (190˚С, 2,16 kg) | 0,921 | ||||
EVA (ethylene-vinyl acetate) | Processing method | |||||
11104-030 | Kazanorgsintez | 3 (190˚С) | Film, technical products | Moulding, extrusion | ||
11306-075 | 7,5 (190˚С) | |||||
11507-070 | 7 (190˚С) | Insulating material, gaskets, adhesive compositions | Moulding, extrusion, compounding | |||
11708-210 | 21 (190˚С) | Additive for petroleum products, composition for parchment and cardboard coating, for containers and food packaging coating | Compounding, extrusion | |||
11808-340 | 34 (190˚С) | |||||
12306-020 | 2 (190˚С) | Heat-shrinkable film, composition for parchment and cardboard coating, for containers and food packaging coating | Moulding, extrusion, compounding | |||
12206-007 | 1 (190˚С) | Moulding, extrusion, compounding | ||||
HPP for CPP film | ||||||
PP H080 CF/2 | NPP Neftekhimia | 8,0 | Well-balanced physical and mechanical properties of finished films | Multilayer non-metallized CPP films for food (grocery, confectionery and bakery products) and non-food (flowers, stationery) packaging | ||
PP H080 CF/5 (PP1316M) | Nizhnekamskneftekhim | 8,0 | ||||
PP H085 CF | NPP Neftekhimia, Polyom | 8,0 | Improved slip and anti-blocking properties of finished films, high gloss and transparency | |||
PP H081 CF/2 | NPP Neftekhimia | 8,0 | Special stabilization formulation that does not contain metal stearates. Improved consumer properties and physical and mechanical characteristics of finished films | Multilayer metallized CPP films for food and non-food packaging | ||
RPP, IPP for CPP film | Polymer type | |||||
PP R080 CF/5 (PP4216M) | Nizhnekamskneftekhim | 8,5 | Well-balanced physical and mechanical properties of finished films. Sealing initiation temperature: from 135ºC | Multi-layer non-metallized CPP films with low requirements for sealing properties (outer sealing layers) | Random | |
PP R085 CF/5 (PP4215M) | 8,5 | Random | ||||
PP R065 CF/5 (PP4225L) | 6,0 | Improved physical and mechanical characteristics, anti-block and slip properties. Lower sealing initiation temperature: from 130ºC | Multilayer non-metallized CPP films with increased requirements for sealing properties (outer welded layers) | Random | ||
PP I013 CF/5 (PP8310G) | 1,6 | Optimal balance of physical and mechanical properties. Excellent welding properties and strength indicators, increased resistance to thermo-oxidative degradation | Processing by extrusion, for use in the inner heat seal layer of multilayer films (retort packaging) | Block | ||
HPP, RPP for BOPP film | Polymer type | |||||
PP H031 BF | Zapsibneftekhim, Polyom, NPP Neftekhimia | 3,0 | Special purpose grade with an enhanced formulation that does not contain metal stearates. Provides high performance and excellent optical properties | Biaxially oriented mono- and multilayer films for food and non-food packaging, including metallized films | Homopolymer | |
PP H036 BF | Zapsibneftekhim | 3,0 | Special purpose grade with an enhanced formulation that does not contain metal stearates. Provides high performance and excellent optical properties. Does not contain phthalates | Homopolymer | ||
PP R060 BF/5 | Nizhnekamskneftekhim | 6,0 | Lower melting point and thermal welding point (sealing initiation temperature: 130ºC) | Multilayer biaxially oriented films, including metallized films (outer welded layers) | Random | |
(PP4222L) |
Conclusion
Flexible polyolefin packaging became popular in the middle of the last century, and it is still irreplaceable in many applications. In this article, we have just begun examining the properties of polyolefins and the ways of using them to manufacture films. Later on, we plan to look at technologies for processing polyolefins into films, the main types of films as well as various details of their manufacturing processes and uses.
Comments (0)