Полимеры применяются во многих элементах автомобилей – от бамперов и фар до приборных панелей и обшивки салона. Массовое внедрение полимеров в автомобилестроении стало настоящей революцией, обусловив ряд значимых изменений в характеристиках машин.
Замена традиционных материалов полимерами позволила значительно снизить вес автомобилей. Это положительно сказывается на экономии топлива и уменьшении выбросов углекислого газа. Благодаря деформируемости, полимерные элементы способны поглощать энергию удара, повышая тем самым уровень безопасности. Применение полимеров позволяет оптимизировать производство многих деталей, снижая стоимость автомобилей. Полимерные компоненты можно подвергать вторичной переработке. Из полимеров легко изготавливать детали, имеющие сложную форму, что дает свободу для дизайнеров.
Анализ применения полимеров в транспортных средствах показывает, что наибольшая доля этих материалов (96% по массе) используется в автомобилях и только 4% – в железнодорожном, воздушном и водном транспорте. Это объясняется массовым производством автомобилей по сравнению с остальными видами транспорта.
Автомобильная индустрия постепенно переориентируется на электромобили, эта тенденция особенно выражена на азиатском рынке. В электромобиле примерно на 100 кг больше пластика по сравнению с обычным автомобилем такого же массогабаритного класса. В России основной интерес потребителей остается на стороне автомобилей с двигателями внутреннего сгорания (ДВС), что обусловлено климатом, традициями и многими другими факторами.
По прогнозу аналитиков СИБУРа, к 2030 году объемы российского производства автомобилей с ДВС увеличатся на 20% относительно уровня 2020 года.
В ответ на растущий спрос СИБУР разрабатывает перспективные материалы для автомобилестроения, включая специальные марки поликарбоната и АБС-пластика. Для производства одного автомобиля в среднем требуется около 18 кг этих материалов (6–9% от веса автомобиля). Они используются для изготовления фар, задних фонарей, приборных панелей и других деталей. Ожидается дальнейший рост потребления поликарбоната и АБС-пластика, особенно в коммерческом транспорте.
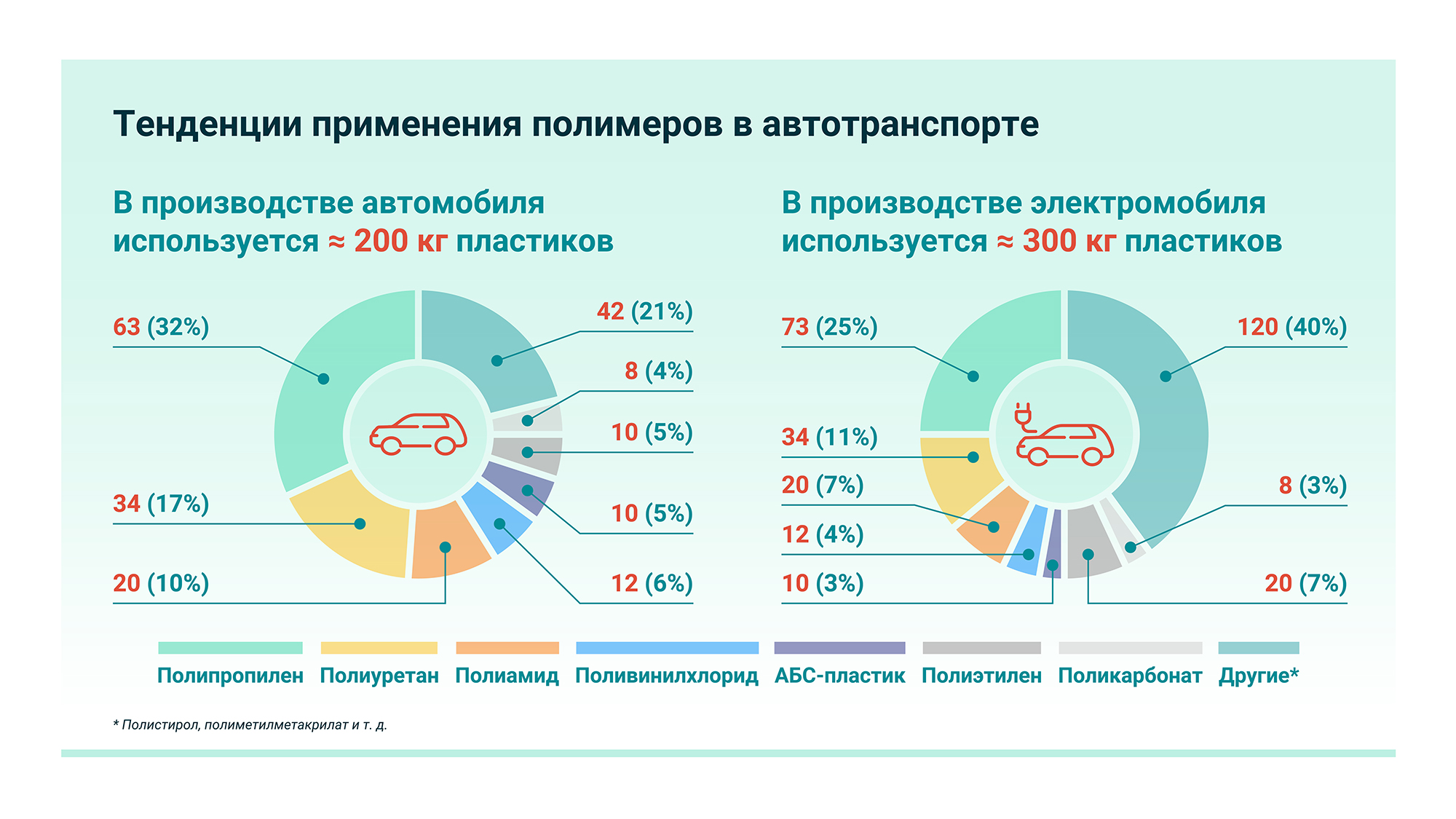
Поликарбонат
Поликарбонат – полимерный материал, широко применяемый в производстве деталей интерьера и экстерьера автомобилей. Его преимущества, такие как прочность, легкость, термостойкость и светопропускаемость, делают его почти идеальным для замены традиционных материалов. Внутри салона поликарбонат используется, например, для изготовления приборных панелей – легких, прочных и устойчивых к царапинам. Он позволяет дизайнерам создавать сложные формы, которые эстетичны и функциональны.
Поликарбонат применяется и во внешних элементах автомобиля, таких как бамперы, накладки на кузов и фары. Автомобильные фары испытывают постоянное воздействие внешней среды, поэтому для их изготовления особенно важно использовать устойчивые материалы. Поликарбонат отвечает этим требованиям. Он достаточно прочный, термостойкий, хорошо переносит как высокие, так и низкие температуры, в том числе с резкими перепадами. Высокая светопропускаемость – еще одна важная характеристика поликарбоната, она составляет более 90%. Кроме того, фары из поликарбоната разбиваются на крупные осколки без острых краев, что снижает риск травм и повреждения внутренних элементов фары.
СИБУР на постоянной основе ведет направленную разработку специализированных автомобильных материалов в соответствии с требованиями заказчиков. Одной из новейших разработок стала марка поликарбоната PC-022 URC1, которая по своим характеристикам не уступает иностранным аналогам. Этот прозрачный материал обладает требуемым оттенком цветности, высокой устойчивостью к УФ-излучению, жесткостью, отличными характеристиками ударной вязкости. Литьевые изделия из этого полимера легко снимаются с формы, что облегчает производство фар. Непосредственное сравнение образцов фар, изготовленных из импортного сырья и из PC-022 URC1, показало, что российская марка не уступает импортным по реологическим, цветовым, оптическим и физико-механическим показателям. При проведении испытаний в климатической установке, имитирующей погодные условия, поликарбонат PC-022 URC1 показал на 30% большую устойчивость, чем аналогичный импортный пластик (это определяется по изменению индекса желтизны и голубизны).
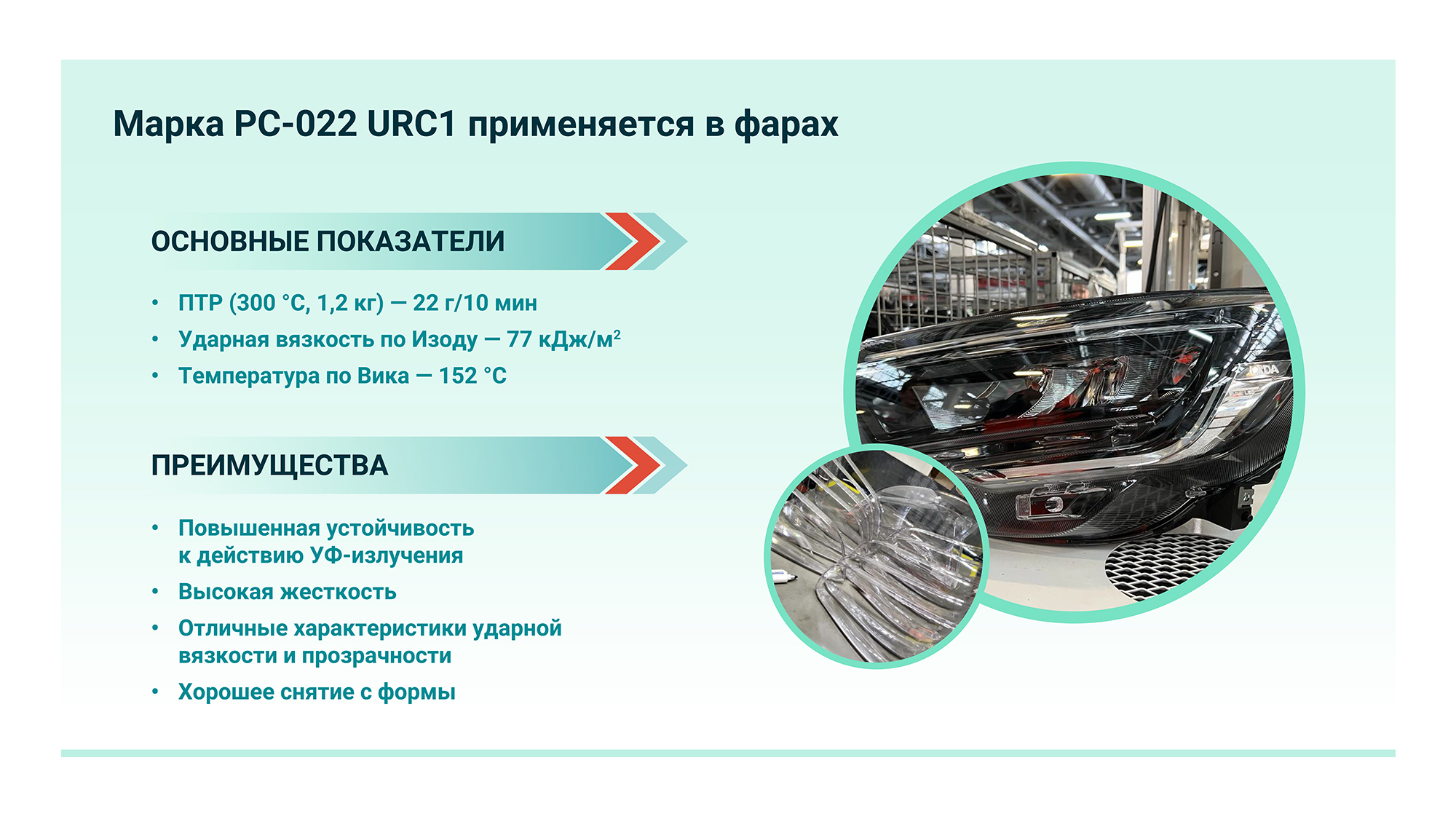
Другим перспективным направлением развития марочного ассортимента поликарбоната является импортозамещение трудногорючих марок ПК, применяемых для автобусов и ж/д транспорта, и разработка ПК молочного цвета, который применяется для изготовления плафонов внутреннего освещения автомобиля.
АБС-пластик
Помимо поликарбоната, СИБУР производит автомобильные марки АБС-пластика (АБС-пластики представляют собой сополимеры, получаемые в результате полимеризации стирола и акрилонитрила в присутствии бутадиена). Эти материалы обладают рядом преимуществ, таких как:
- устойчивость к резким ударам и низким температурам благодаря наличию в структуре бутадиеновых фрагментов;
- допустимый уровень теплостойкости (до 100°C), что позволяет использовать его для производства изделий, подвергающихся локальному нагреву;
- стойкость к щелочам, бензину и неорганическим солям;
- хорошая окрашиваемость, что важно для применения в автомобилестроении.
Барьерами для более широкого применения этих материалов можно считать невысокую атмосферостойкость, недостаточные электроизоляционные свойства и относительно невысокий уровень теплостойкости. На данный момент СИБУР ведет активную работу для устранения указанных недостатков с помощью различных стабилизирующих добавок.
Особо стоит отметить литьевую марку АБС 3432, которая используется при изготовлении корпуса заднего фонаря. Эта марка обладает следующими характеристиками:
- высокое значение ПТР (220°C, 10 кг) – 33 г/10 мин;
- сбалансированное соотношение ударной вязкости по Изоду (14 кДж/кв.м) и температуры по Вика (90°C).
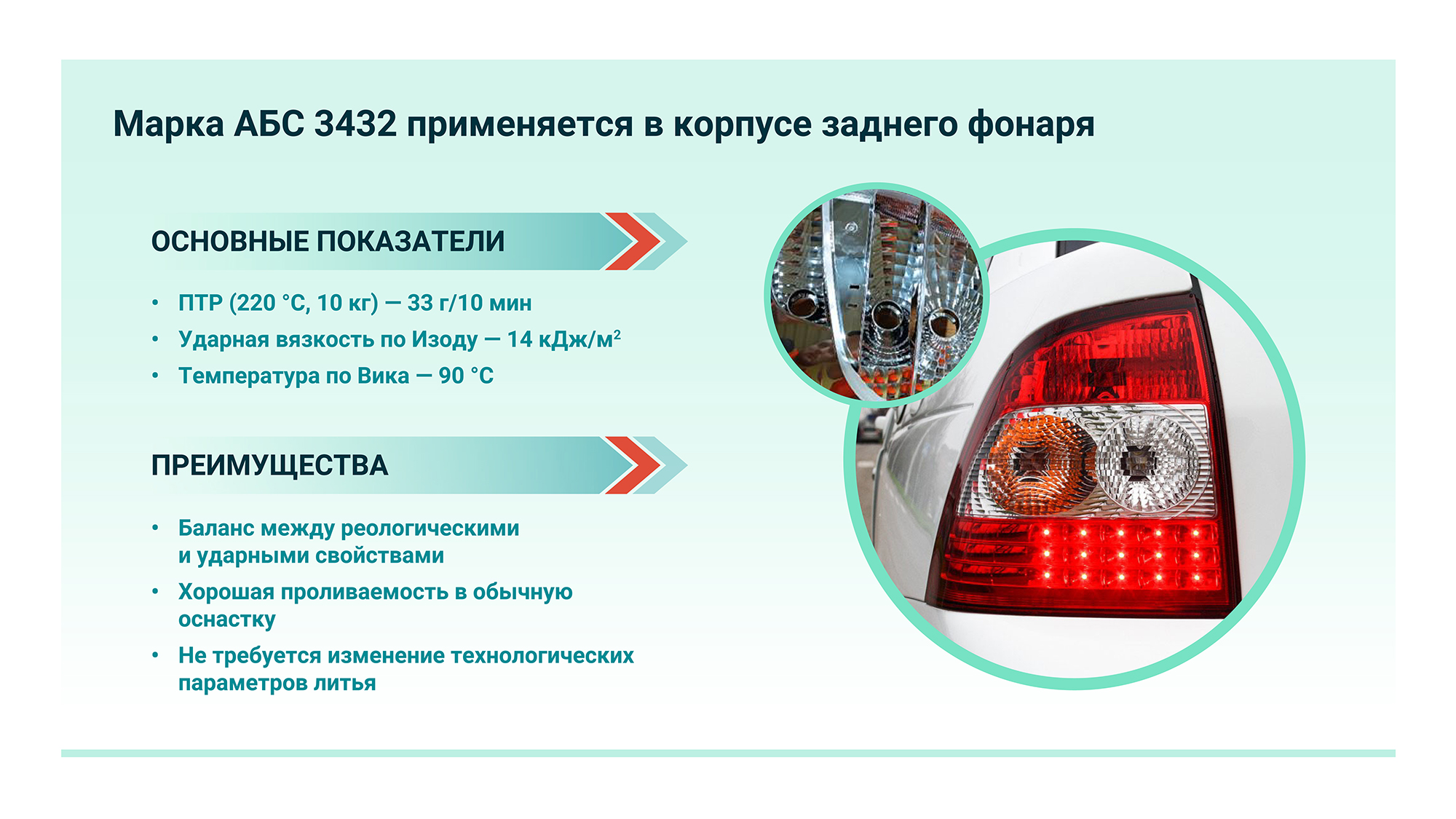
Эти характеристики позволяют изготавливать корпуса автомобильных фонарей без изменений в обычных технологических параметрах литья, что является важным требованием при переходе на новое сырье, ведь любые изменения оснастки или схемы производства являются весьма трудоемкими и дорогостоящими. В настоящее время АБС 3432 проходит необходимую сертификацию для использования в транспортных средствах на постоянной основе.
СИБУР изучает возможности создания теплостойких (более 100°C) марок АБС-пластика, это одно из приоритетных направлений разработок. Также проводятся исследования по улучшению определенных свойств АБС-пластика с учетом требований заказчиков. Например, для деталей экстерьера требуется улучшить качество окрашиваемости, повысить ударную прочность по методу Изода и улучшить температуру изгиба под нагрузкой (HDT). Для изготовления автомобильных молдингов также необходимо обеспечить хорошее нанесение гальванопокрытия, что представляет собой нетривиальную задачу. В настоящее время СИБУР активно работает над этими проектами.
СИБУР ведет работу, направленную на внедрение в цепочку поставок автомобильных заводов больших объемов российского сырья для производства автомобильных комплектующих. Разработчики улучшают характеристики существующих марок полимеров, учитывая стандарты качества автомобильной промышленности и потребности заказчиков. СИБУР предлагает широкий спектр решений для автопрома, основанных на поликарбонате, компаундах и АБС-пластике. Новые разработки компании позволяют улучшить характеристики полимеров, делая их более легкими, прочными, экологичными и функциональными.
Комментарии (0)