The polymer market-leading SIBUR first got involved in developing new industrial technologies of recycling post-consumer polymer waste under its 2025 Sustainability Strategy. This year, the market welcomed the arrival of the new brand Vivilen, a blend of compounds that contains 25% to 50% recycled polymers.

Today, socially responsible companies across the world are committing to use a certain share of recycled materials in production. Major brands have set 2025 and 2030 as the target dates for transitioning to more environmentally-friendly technologies. This powerful trend brings the idea of the circular economy to life. Once business generates demand for these products, polymer recycling will become a socially responsible and profitable business.
According to Elena Maltseva, Senior Expert, Product Marketing at SIBUR, the biggest advantage of SIBUR’s compounds is the fact that they allow manufacturers to use recycled products without compromising on the quality of a virgin material.
THIS YEAR, THE MARKET WELCOMED THE ARRIVAL OF THE NEW BRAND VIVILEN, A BLEND OF COMPOUNDS THAT CONTAINS 25% TO 50% RECYCLED POLYMERS
“The cases of our partners confirm that. It is safe to use Vivilen to manufacture packaging without the need to invest in equipment or staff retraining. Our compounds simply replace virgin polymer feedstocks, giving processers a product with a predictable level of quality and their customers packaging with the desired properties.”
Recycled polymers are in trend
In December 2021, PPG Tikkurila announced that its Tikkurila Euro paints would be launched on the Russian market in packaging containing recycled plastic. The packaging for these paints is made of Vivien, a material developed and supplied by SIBUR.
Recycled polymers comprise up to 25% of the packaging for the Tikkurila Euro range, which includes 8 products across 35 SKUs. An appropriate label will be placed on the brand’s new packaging to inform the customer that it contains recycled materials. Even though it entails a production cost increase to the manufacturer, ultimately, the end consumer price of Tikkurila paints will not change. Mir Upakovki (World of Packaging) manufactures this Vivilen packaging.
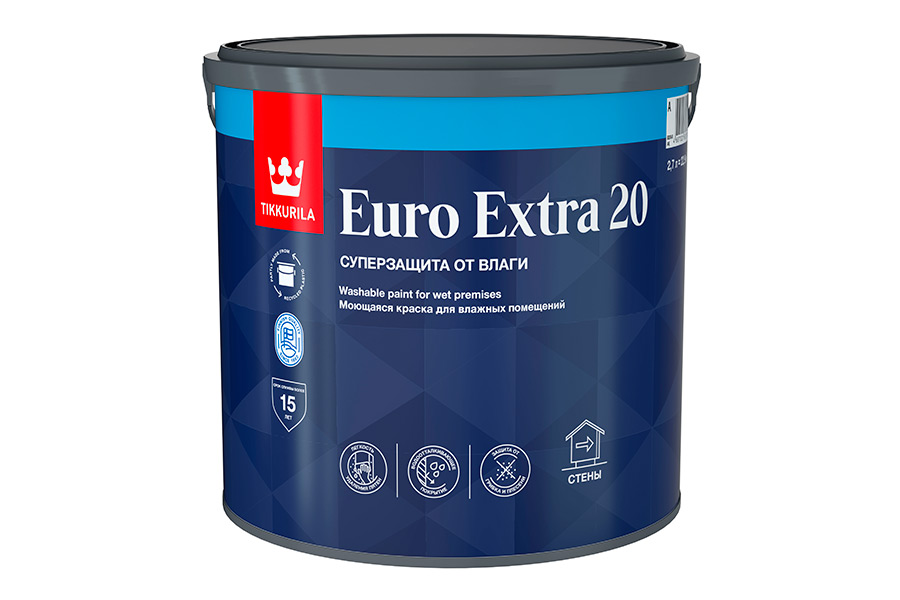
“As the leader of interior and architectural solutions, Tikkurila has been among the pioneers in introducing new technologies to the market,” said Ekaterina Balon, Marketing Director at Tikkurila Russia, Central Asia and China. “We know that other manufacturers take cues from our best practices, so we are confident that by transitioning to post-consumer recycled (PCR) plastic packaging will also send a signal to other market players,” she added. “Consumers are increasingly seeking sustainable initiatives and expect business to support broad environmental action. We hope that other manufacturers will join us and switch to PCR plastic packaging as well. I would like to stress that we are not looking for economic upside from this switch to PCR plastic packaging. Our objective is to reduce our environmental footprint and raise awareness across the market,” said Ekaterina Balon.
THERE ARE TWO TYPES OF VIVILEN COMPOUNDS ON THE MARKET TODAY: RPE (POLYETHYLENE-BASED GRANULES) AND RPP (POLYPROPYLENE-BASED ONES). THEY ARE USED TO MANUFACTURE HEAT-SHRINK FILM, PACKAGING FOR HOUSEHOLD CHEMICALS, BUCKETS, JERRY CANS, AND PLASTIC CONTAINERS
Mir Upakovki highlighted the fact that it has set itself the ambitious target of becoming a leader in using recycled materials and building a plastic recycling loop. Its range of traditional cylindrical and handheld buckets made from a PCR-based solution and featuring in-mould labels has allowed its key partner PPG to enter the paints and coatings market with eco-friendly, reliable, and attractive products for consumers who care about the environment and value high quality. During product launch, the Mir Upakovki team conducted large-scale testing on the new material to finetune its innovative product ranges and secure top product quality and stability for key industry partners.” The Mir Upakovki team is confident that the new packaging solution is fully aligned with its sustainability agenda and its partners’ strategies.
According to experts, there are two types of waste: Post-industrial recycled (PIR) and post-consumer recycled (PCR). The first type is production waste: rejects, cuttings, etc. and has, on the whole, long been recycled. The second type is consumer waste, which in most cases is landfilled. Recycling PCR polymers is a complicated and costly process, but Vivilen compounds tackle this challenge head-on.
ESG solutions for business
PPG Tikkurila’s packaging containing recycled polymers is the second high-profile use case for SIBUR’s Vivilen compounds (link: https://vivilen.sibur.ru) in the Russian market. The anticorrosion and flame resistant material producer O3 was the first to try out Vivilen. Thanks to a collaboration between the packaging manufacturer Jokey, O3 and SIBUR, paint packaging containing Russian PCR materials is now being manufactured and is on the market.
“This is a big milestone for green packaging in Russia and a response to the growing consumer demand for eco-friendly and conscious consumption,” said Gregory Shifrin, General Director of O3 Group. “The use of recycled polymers helps implement projects promoting the circular economy. In the near term, consumers will ask for more information on manufacturers’ environmental contribution, the progress they are making towards making packaging reusable and recyclable and closing its recycling loop, and much more. Looking at the future of SIBUR’s new compound, we can say that by choosing recycled polymer packaging we reduce the amount of virgin plastic being produced globally and cut our carbon footprint,” he explained.
Alexey Sboev,
SIBUR’s Head of Marketing, Petrochemicals
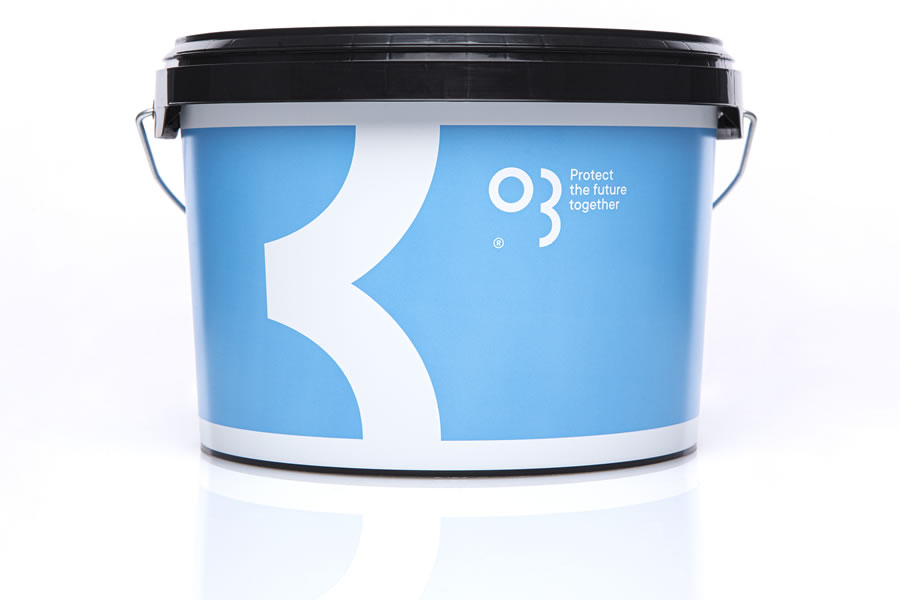
The different types of compounds
There are two types of Vivilen compounds on the market today: rPE (polyethylene-based granules) and rPP (polypropylene-based ones). They are used to manufacture heat-shrink film, packaging for household chemicals, buckets, jerry cans, and plastic containers. Due to specific legislative requirements, this kind of packaging can only be used for non-food products.
“Vivilen compounds have just entered the market and they are being integrated into our partners’ production systems as we speak,” said Elena Maltseva. “Next year we will be able to tell you much more about its new and exciting applications.”
BY 2030, SIBUR PLANS TO PRODUCE AT LEAST 250,000 TONNES OF LOW-CARBON PRODUCTS AND PRODUCTS CONTAINING RECYCLED OR BIO-BASED MATERIALS ANNUALLY
Another important event in the pipeline is the launch of the third Vivilen-branded compound – rPET (polyethylene terephthalate-based granules). New rPET capacity is now being constructed at SIBUR’s POLIEF site, supported by the Industrial Development Fund. The main benefit of this compound is that it can be used in food packaging. Producers of mineral water, as well as alcoholic and non-alcoholic beverages will soon have the opportunity to manufacture PET packaging containing recycled materials.
Alexander Grishkov,
Senior Director Sustainability, PepsiCo Ru-BUCCA
“We expect incremental progress. The notion of the circular economy has two components, and both are equally important. With the increase in demand, we will see further development of waste sorting and reuse, which will make raw materials with recycled content more economically attractive. Our estimates show that by 2025 SIBUR will be able to facilitate the recycling of at least 100,000 tonnes of polymer waste annually as part of its investment projects and through collaboration with partners. By 2030, SIBUR will be able to produce at least 250,000 tonnes of low-carbon products containing recycled or bio-based materials annually,” noted Elena Maltseva.
Modern polymer recycling solutions are based on mechanical recycling technology. Compounds are made of mechanically crushed and cleaned polymer waste, virgin granules, and additives to ensure consistent quality. SIBUR’s next step will be to explore chemical recycling technology. It will enable the Company to recycle mixed, multicomponent, and contaminated PCR plastic waste, and increase the share of recycled polymers in our feedstock. The new technology will help produce plastics with properties indistinguishable from those made of virgin polymers, unlocking an unlimited number of recycling cycles. SIBUR’s R&D teams predict that these solutions are five to seven years out.
Also read the article Forbes
Comments (0)